Role of Advanced Welding and Slitting Machine in Tin Can Manufacturing
In food and beverage packaging, tin cans continue to be a staple due to their durability, cost-effectiveness, and ability to preserve contents. The process of manufacturing these cans, however, has evolved dramatically over the years, with advancements in technology making production more efficient and precise. At the heart of modern tin can manufacturing are key pieces of equipment such as automatic can body welding machines, tinplate slitting knives, and automatic trimming machines, which ensure a high-quality finished product.
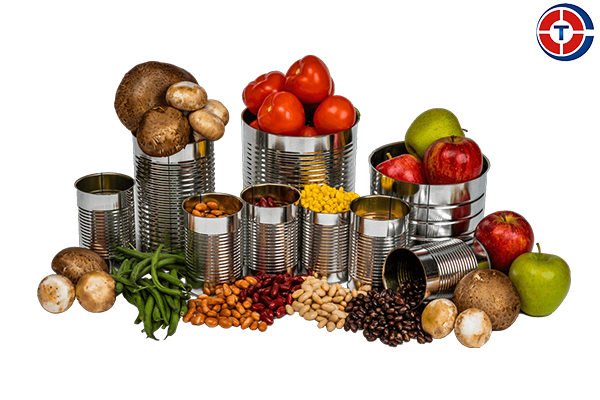
One of the most significant developments in the tin can production line is the automatic can body welding machine. These machines play a crucial role in joining the cylindrical body of the can by welding the metal seams, typically using materials like tinplate, iron plate, chrome plate, galvanized plate, and stainless steel. Modern welding machines from manufacturers like Changtai Intelligent are designed for speed and precision, increasing throughput and reducing the likelihood of defects. These machines are programmed to weld the seams with high accuracy, which is critical for ensuring the structural integrity of the can.
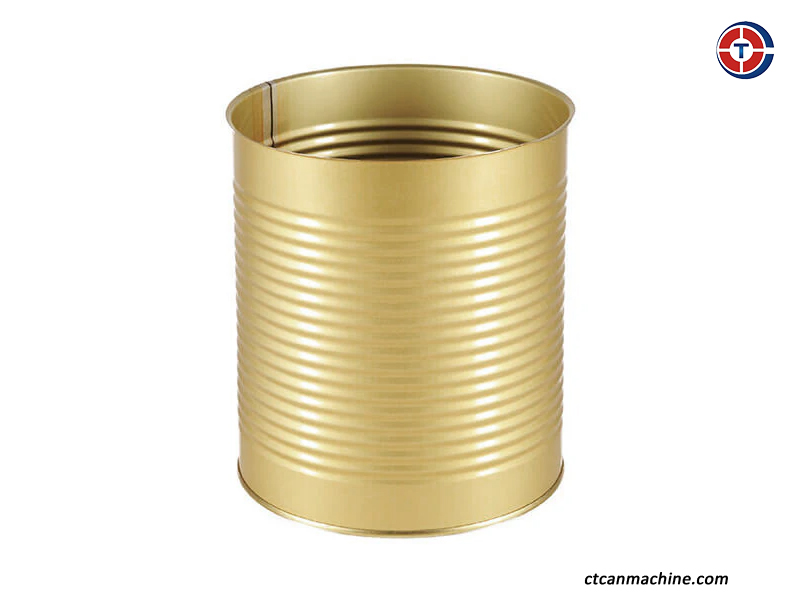
key advantages
The automatic can body welding machine offers several key advantages that make it an essential piece of equipment in modern can manufacturing:
● Increased Production Speed: Automatic welding machines significantly reduce the time required to join the metal sheets, increasing the overall speed of the production process. This enables manufacturers to produce large volumes of cans in a short period, improving efficiency and meeting higher demand.
● High Precision and Consistency: These machines are designed for precise welding of the metal seams, ensuring a consistent and uniform weld across all cans. The accuracy of automatic welding machines helps eliminate defects like weak or uneven seams, which could compromise the structural integrity of the cans.
● Reduced Labor Costs: Since the process is automated, the need for manual labor is greatly reduced. This not only cuts down on labor costs but also minimizes human error, leading to more consistent production quality. Operators only need to monitor the machine, which reduces the risk of errors and accidents.
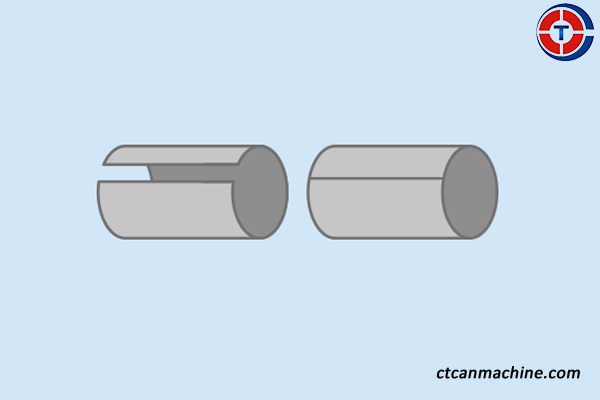
● Energy Efficiency: Modern welding machines are often designed with energy-saving features that optimize power usage during the welding process. This reduces operational costs and contributes to more sustainable manufacturing practices.
● Improved Quality Control: With advanced features like automated seam inspection and control systems, these machines can detect defects during production, ensuring that only cans meeting quality standards move on to the next stage of the process. This continuous monitoring enhances the overall quality of the finished product.
● Lower Maintenance Costs: Many automatic welding machines are built with durable, high-quality components that require less frequent maintenance compared to older, manual models. Regular automated diagnostics also help identify potential issues before they lead to downtime or costly repairs.
● Integration with Other Equipment: These welding machines can be seamlessly integrated into an automated production line, working in conjunction with other machinery like slitting machines, trimming machines, and coating equipment. This creates a streamlined, efficient production process that reduces bottlenecks and improves throughput.
● Flexibility for Customization: Many automatic can body welding machines can be adjusted to accommodate different can sizes and specifications. This flexibility makes it easier to customize production runs to meet specific market needs, whether for small batch or large-scale production.
Automatic can body welding machines provide a range of benefits that improve efficiency, reduce costs, and enhance product quality, making them a vital component in modern can manufacturing.
After the welding process, the metal sheets are then subjected to slitting to produce narrower strips that will form the cylindrical bodies. Tinplate slitting knives are essential in this step, cutting the metal sheets with exacting precision. The quality of these knives, often made of high-grade materials like carbide, directly impacts the accuracy of the slitting process and the overall quality of the can bodies. Companies like Huxin Cemented Carbide specialize in producing these carbide blades, which are known for their sharpness, wear resistance, and long lifespan.
Together, these technologies streamline the tin can production process, allowing manufacturers to produce high-quality cans at a rapid pace. As consumer demand for reliable and sustainable packaging grows, the industry continues to invest in cutting-edge machinery that ensures both efficiency and precision. From welding to slitting and trimming, the use of advanced equipment in tin can manufacturing is paving the way for a new era of packaging solutions.
China leading provider of 3 piece Tin Can Making Machine and Aerosol Can Making Machine.
Changtai Intelligent Equipment Co., Ltd.is an experienced Can Making Machine factory.Including parting, shaping, necking, flanging, beading and seaming,Our can making systems feature high-level modularity and process capability and are suitable for a wide range of applications,
With fast, simple retooling, they combine extremely high productivity with top product quality, while offering high safety levels and effective protection for operators.
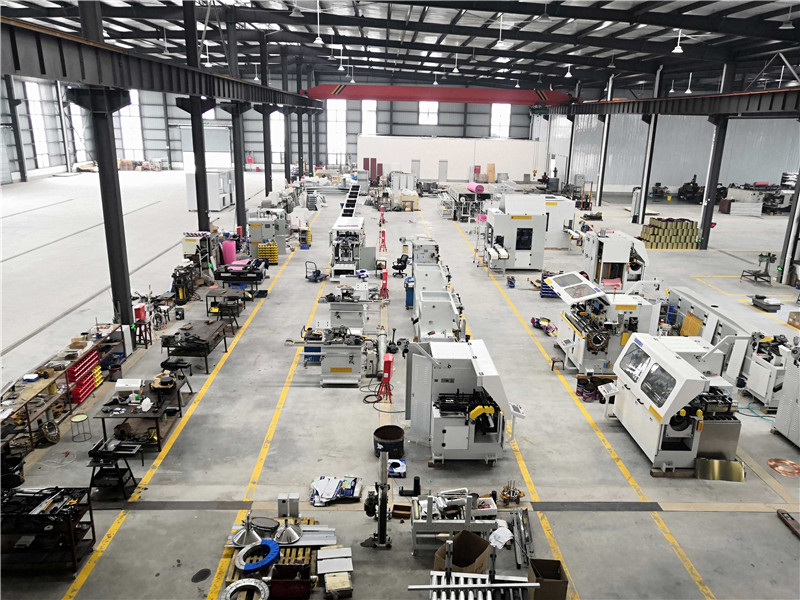
Know more
To know more about prices and services, please click here>>> Contact us
--------
To know more about our Company, please click here>>> About us
--------
To know more about our portfolio, please click here>>>Our Products
--------
To know more about our AfterSales and other People also ask questions, please click here>>> FAQ
--------
View products > > > Link: Can making equipment...
Post time: Jun-12-2025