The Evolution and Efficiency of 3-Piece Can Making Machines
In the ever-evolving landscape of packaging, the 3-piece can remains a staple in the industry, known for its durability and versatility. The can manufacturing process has seen significant advancements, especially in the realm of 3-piece can making machines, which have transformed how these essential containers are produced.
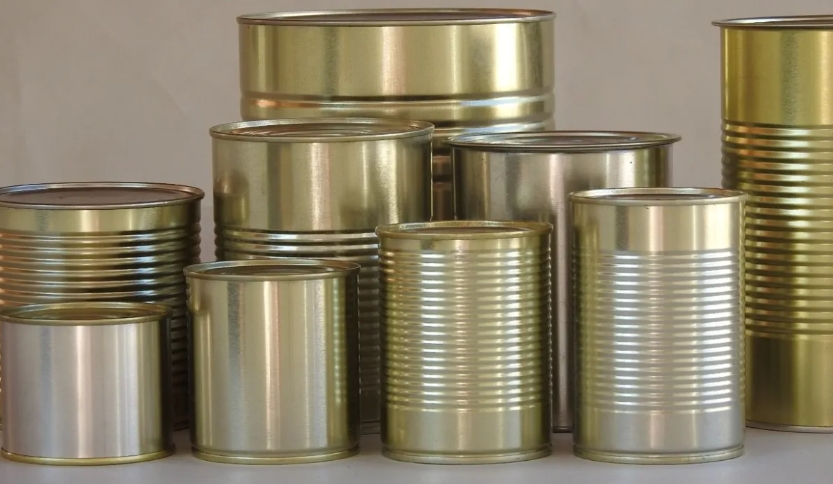
At the core of the 3-piece can design are its three fundamental components: the can body, welded seams, and end closures. The can body is typically formed from sheet metal, providing strength and protection for the contents inside. The process begins with the careful selection of raw materials, as the quality of the metal plays a crucial role in the durability and performance of the final product.
Modern can forming techniques have revolutionized production lines, enabling manufacturers to produce cans at unprecedented speeds. High-speed operation is a hallmark of contemporary machinery, allowing companies to meet the growing demand for metal cans across various sectors, from beverages to food packaging. Automation has become a key player in this evolution, streamlining processes and reducing the need for manual labor, ultimately enhancing efficiency.
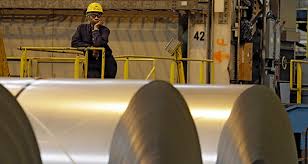
Quality control is paramount in can manufacturing, ensuring that every can produced meets industry regulations and safety standards. Advanced technologies are employed to monitor the integrity of welded seams and the precision of can body dimensions. This focus on quality not only guarantees a reliable product but also fosters consumer trust in the brands that utilize these cans.
Equipment suppliers have recognized the importance of customization in the production of 3-piece cans. Each manufacturer may have unique requirements based on their product lines, leading to innovations in machinery that allow for tailored solutions. This flexibility ensures that businesses can adapt to market changes and consumer preferences without compromising on quality or efficiency.
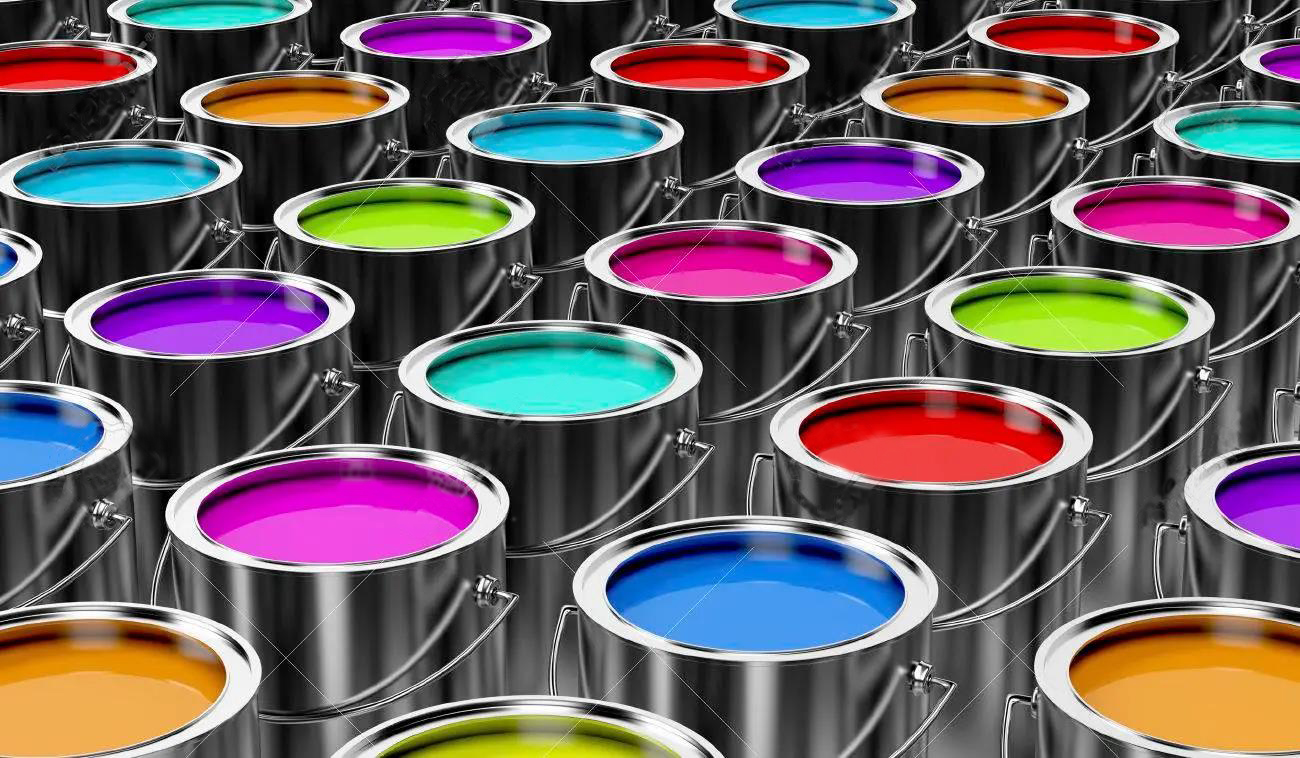
Moreover, the coating process is essential in the can making industry. Protective coatings are applied to metal surfaces to prevent corrosion and enhance aesthetic appeal. This step is critical, especially in industries where cans are exposed to harsh environments or require a specific branding approach. The integration of advanced coating technologies within the manufacturing process further underscores the commitment to quality and longevity in 3-piece can production.
While the benefits of modern 3-piece can making machines are clear, maintenance remains a vital aspect of ensuring longevity and performance. Regular upkeep of machinery not only prolongs its life but also prevents production downtime, which can be costly for manufacturers. Adhering to maintenance schedules and investing in proper training for staff are crucial steps in maximizing the efficiency of production lines.
In conclusion, the journey of 3-piece can manufacturing has been marked by innovation and adaptability. As consumer demands evolve, so too do the technologies and processes that shape the industry. By embracing automation, prioritizing quality control, and allowing for customization, manufacturers are equipped to deliver reliable, high-quality metal cans that meet the ultimate standards of safety and efficiency. The future of 3-piece can making machines is bright, promising continued growth and advancement in the packaging sector.
Related Video of Tin Can Welding Machine
Chengdu Changtai Intelligent Equipment Co., Ltd.- A automatic can equipment Manufacturer and Exporter, provides all the solutions for Tin can making. To know the latest news of metal packing industry, Find new tin can making production line, and get the prices about Machine For Can Making,Choose Quality Can Making Machine At Changtai.
Contact us for details of machinery:
Tel/Whatsapp:+86 138 0801 1206
Email:NEO@ctcanmachine.com
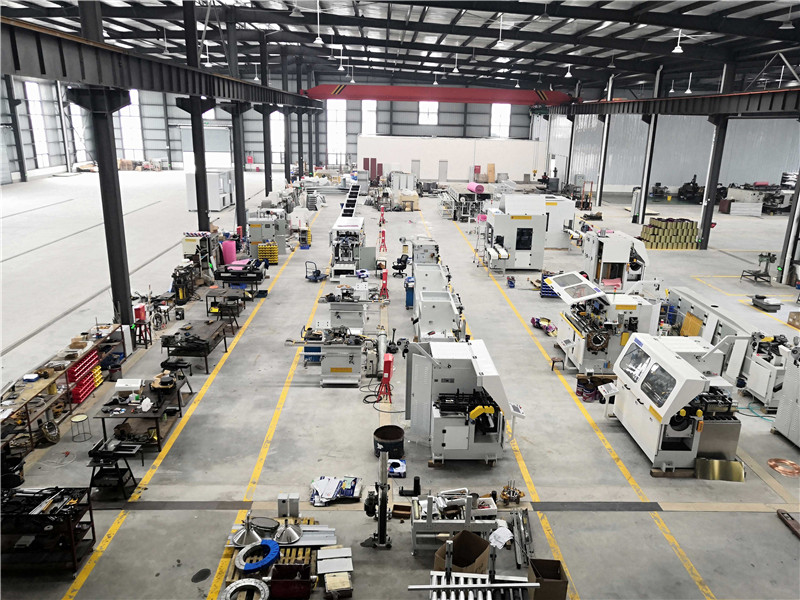
Post time: Oct-24-2024