Maintenance of Automatic Can-Making Production Lines
Automatic can-making production lines, including can-making equipment such as can body welders, save substantial time and costs. In industrially advanced cities, the maintenance of these automated lines has become a key focus. The maintenance process primarily relies on both operators and maintenance technicians working together to ensure smooth operation.
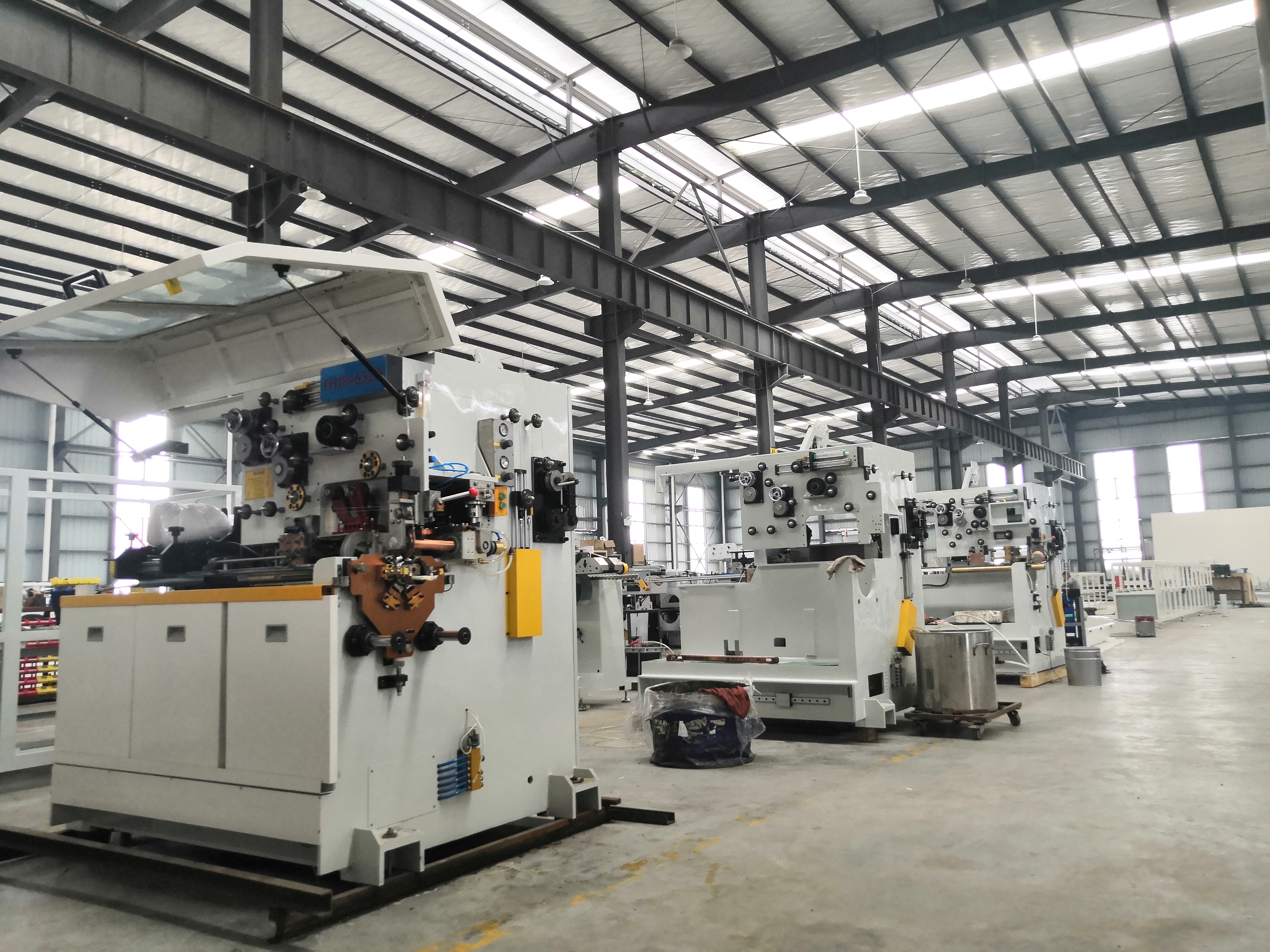
Two Major Methods of Automatic Production Line Maintenance:
- Synchronous Repair Method: If a fault is detected during production, immediate repairs are typically avoided, and temporary measures are taken to maintain operations. This method enables the production line to continue until a holiday or scheduled downtime, at which point maintenance technicians and operators can collaborate to address all issues simultaneously. This ensures that equipment, such as the can body welder, can operate at full capacity on Monday when production resumes.
- Segmented Repair Method: For larger issues that require extended repair time, the synchronous repair method may not be feasible. In such cases, repairs are conducted on specific sections of the automatic can-making line during holidays. Each section is repaired progressively, ensuring the production line remains in operation during working hours. Additionally, a proactive approach to maintenance is advised. By installing timers to log operational hours, wear patterns of components can be predicted, allowing for the preemptive replacement of easily worn parts. This helps avoid unexpected faults and maintains the production line’s high efficiency.
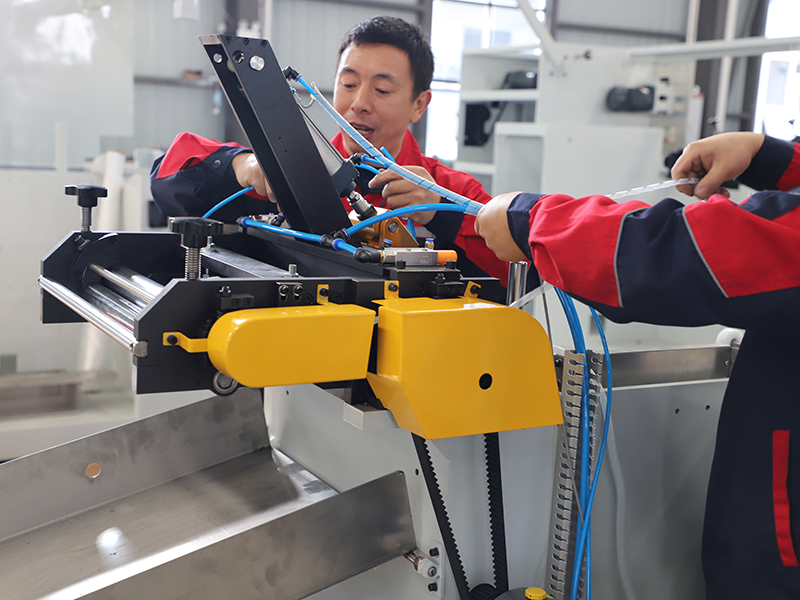
Maintenance of the Automatic Production Line:
- Routine Checks: Electrical circuits, pneumatic lines, oil lines, and mechanical transmission parts (e.g., guide rails) should be inspected and cleaned before and after each shift.
- In-Process Inspections: Regular patrol inspections should be conducted, with spot checks on critical areas. Any irregularities should be documented, with minor issues addressed promptly and larger issues prepared for during shift changes.
- Unified Shutdown for Comprehensive Maintenance: Periodically, a full shutdown is organized for extensive maintenance, focusing on replacing worn components in advance to prevent potential breakdowns.
- The automatic production line, sometimes called an "automatic line," comprises a workpiece transfer system and control system that link a group of automated machines and auxiliary equipment in sequence to complete part or all of a product’s manufacturing process. Advances in numerically controlled machines, industrial robotics, and computing technology, along with group technology applications, have enhanced the flexibility of these lines. They now support automated production of various product types in small to medium quantities. This versatility has led to a widespread adoption in the machinery manufacturing sector, pushing automatic can-making lines towards even more advanced and flexible manufacturing systems.
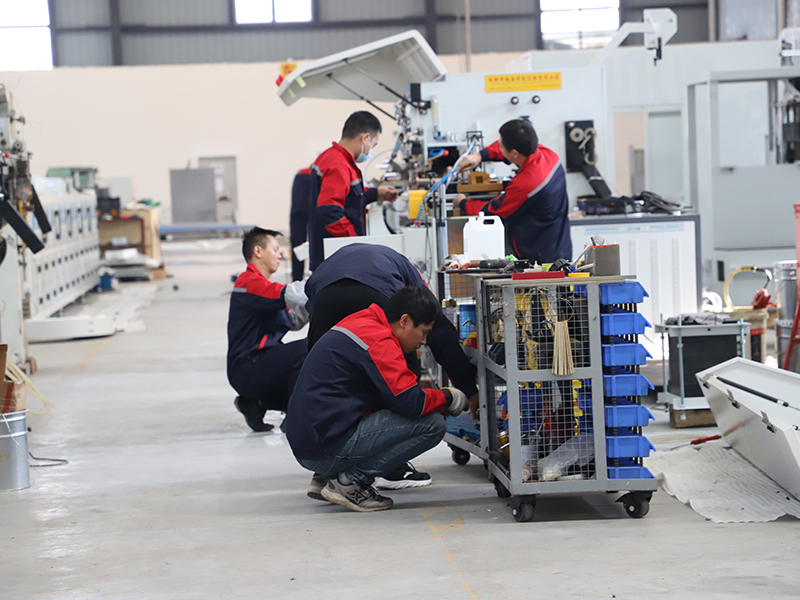
Chengdu Changtai Intelligent Equipment Co., Ltd.- A automatic can equipment Manufacturer and Exporter, provides all the solutions for Tin can making. To know the latest news of metal packing industry, Find new tin can making production line, and get the prices about Machine For Can Making,Choose Quality Can Making Machine At Changtai.
Contact us for details of machinery:
Tel:+86 138 0801 1206
Whatsapp:+86 134 0853 6218
Email:tiger@ctcanmachine.com CEO@ctcanmachine.com
Post time: Nov-01-2024