main production process for the body of a three-piece food can
The main production process for the body of a three-piece food can includes cutting, welding, coating and drying of the weld seam, necking, flanging, beading, sealing, leak testing, full spraying and drying, and packaging. In China, the automatic can production line is typically composed of body assembly machines, bi-directional shearing machines, welding machines, weld seam protection and coating/curing systems, interior spraying/curing systems (optional), online leak detection machines, empty can stacking machines, strapping machines, and film wrapping/heat shrinking machines. Currently, the body assembly machine can complete processes such as slitting, necking, expanding, can flaring, flanging, beading, first and second seaming, at a speed of up to 1200 cans per minute. In the previous article, we explained the slitting process; now, let's analyze the necking process:
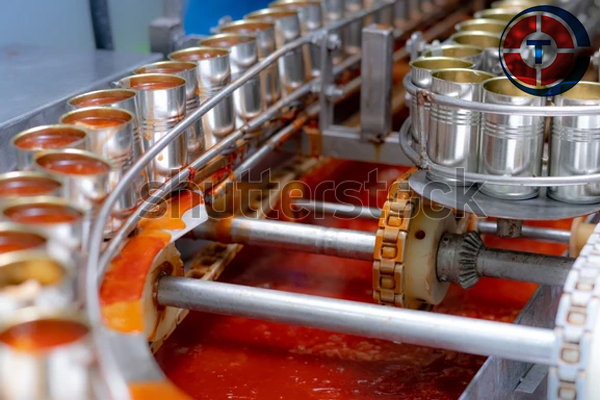
Necking
One important method to reduce material consumption is by thinning the tinplate. Manufacturers of tinplate have done significant work in this regard, but simply thinning the tinplate to reduce can cost is limited by the pressure-resistance requirements of the can structure, and its potential is now quite small. However, with advancements in necking, flanging, and can expansion technology, there have been new breakthroughs in reducing material consumption, especially in both the can body and the lid.
The primary motivation for producing necked cans was initially driven by the desire for product upgrades by manufacturers. Later, it was discovered that necking the can body is an effective way to save material. Necking reduces the diameter of the lid, thus reducing the blanking size. At the same time, as the strength of the lid increases with the reduced diameter, thinner materials can achieve the same performance. Additionally, the reduced force on the lid allows for a smaller sealing area, further reducing the blanking size. However, thinning the can body material may cause issues due to changes in material stress, such as reduced resistance along the can axis and the can body cross-section. This increases the risk during high-pressure filling processes and transportation by fillers and retailers. Hence, while necking does not significantly reduce the can body material, it mainly conserves material on the lid.
Given the influence of these factors and market demand, many manufacturers have improved and upgraded necking technology, establishing its unique position in the various stages of can manufacturing.
In the absence of a slitting process, necking is the first process. After coating and curing, the can body is sequentially delivered to the necking station by the can separation worm and infeed star wheel. At the transfer point, the internal mold, controlled by a cam, axially moves into the can body while rotating, and the external mold, also guided by a cam, feeds in until it matches with the internal mold, completing the necking process. The external mold then disengages first, and the can body remains on the internal mold to prevent slipping until it reaches the transfer point, where it disengages from the internal mold and is delivered to the flanging process by the outfeed star wheel. Typically, both symmetric and asymmetric necking methods are used: the former is applied for a 202-diameter can, where both ends undergo symmetric necking to reduce the diameter to 200. The latter can reduce one end of a 202-diameter can to 200 and the other end to 113, while a 211-diameter can can be reduced to 209 and 206, respectively, after three asymmetric necking operations.
There are three main necking technologies
- Mold necking: The can body’s diameter can shrink at one or both ends simultaneously. The diameter at one end of the necking ring equals the original can body diameter, and the other end equals the ideal necked diameter. During operation, the necking ring moves along the can body's axis, and the internal mold prevents wrinkling while ensuring precise necking. Each station has a limit on how much the diameter can be reduced, depending on material quality, thickness, and can diameter. Each reduction can decrease the diameter by about 3mm, and a multi-station necking process can reduce it by 8mm. Unlike two-piece cans, three-piece cans are not suitable for repeated mold necking due to material inconsistencies at the weld seam.
- Pin-following necking: This technology is derived from two-piece can necking principles. It allows for smooth geometric curves and can accommodate multi-stage necking. The necking amount can reach 13mm, depending on the material and can diameter. The process occurs between a rotating internal mold and an external forming mold, with the number of rotations depending on the necking amount. High-precision clamps ensure concentricity and radial force transmission, preventing deformation. This process yields good geometric curves with minimal material loss.
- Mold forming: In contrast to mold necking, the can body is expanded to the desired diameter, and the forming mold enters from both ends, shaping the final neck curve. This one-step process can achieve smooth surfaces, with material quality and weld seam integrity determining the necking difference, which can reach up to 10mm. Ideal forming reduces tinplate thickness by 5%, but retains thickness at the neck while enhancing overall strength.
These three necking technologies each offer advantages depending on the specific requirements of the can manufacturing process.
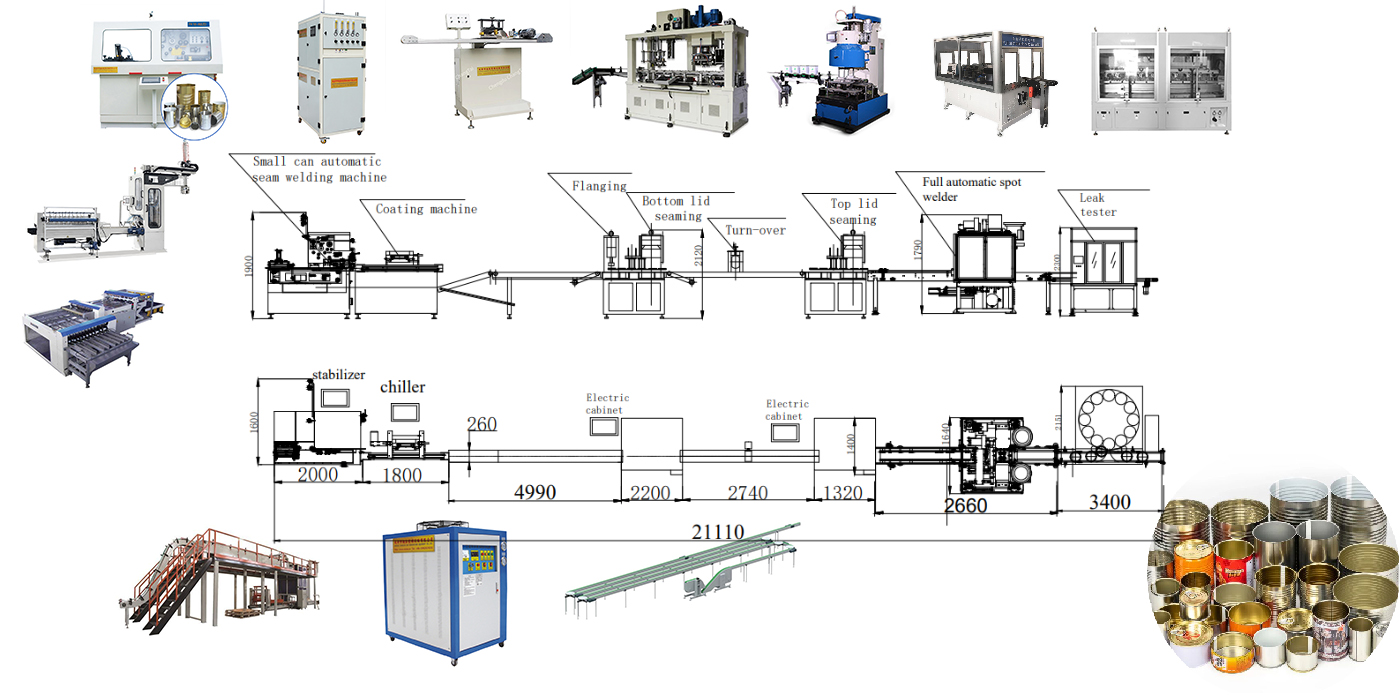
Related Video of Tin Can Welding Machine
Chengdu Changtai Intelligent Equipment Co., Ltd.- A automatic can equipment Manufacturer and Exporter, provides all the solutions for Tin can making. To know the latest news of metal packing industry, Find new tin can making production line, and get the prices about Machine For Can Making,Choose Quality Can Making Machine At Changtai.
Contact us for details of machinery:
Tel:+86 138 0801 1206
Whatsapp:+86 138 0801 1206 +86 134 0853 6218
Email:neo@ctcanmachine.com CEO@ctcanmachine.com
Post time: Oct-17-2024